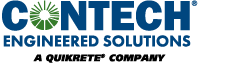
When faced with designing culverts, storm sewers, or underground detention systems, one of the critical decisions you’ll make as the Engineer of Record is pipe selection. Corrugated Metal Pipe (CMP) is often the go-to solution for stormwater applications, and for good reason.
Learn MoreCorrugated steel pipe (CSP) has been a staple in various infrastructure projects due to its strength and flexibility. However, its durability has historically been a point of concern, particularly with galvanized steel, which has shown suboptimal performance in certain environments.
Learn MoreChoosing the right culvert or buried bridge structure is crucial for any site application. While this may seem straightforward, it involves numerous practical and functional considerations. Project engineers and site developers must address these factors early in the planning stages.
Learn MoreMetallic coatings have been applied to iron and steel armaments as early as the 17th century. The purpose of metallic coatings applied to steel is to help retard corrosion. The zinc coating process of steel, referred to as galvanizing, was name after Luigi Galvani, an Italian physicist who lived in the 18th century. Galvanized steel in the construction industry came into widespread use in the early 20th century.
Learn MoreWhen it comes to designing extensive storm sewer conveyance systems, engineers and agencies are constantly seeking innovative alternatives to traditional reinforced box culverts. Contech, a leading player in drainage and stormwater, has been at the forefront of exploring efficient and effective solutions for moving stormwater across the country. While concrete has been the default choice for larger systems, there's a compelling alternative worth considering – Smooth Cor™.
Learn MoreDuroMaxx® SRPE emerges as an important solution for containment needs, offering cost-effectiveness and mitigating schedule impacts caused by supply shortages in the market for FRP, CIP, and pre-cast concrete containment tanks.
Learn MoreHandling and installation of large diameter sewer systems demand meticulous attention due to the increased risks associated with their size and weight.
Learn MoreProper pipe jointing is a critical aspect of designing and installing sanitary sewer systems – especially in the sizeable diameters of 30” and larger. The large joints of these systems play a pivotal role in preventing issues related to infiltration and exfiltration, which can have detrimental effects on the overall functionality of the infrastructure. Inflow and infiltration (I&I) during rain events can lead to capacity issues at wastewater treatment plants, causing severe backups in the system and sanitary sewer overflows (SSOs).
Learn MoreThe notion of bolstering safety factors in pipe design to compensate for subpar installation practices is a complex issue with various considerations. The effectiveness of buried flexible metal and plastic pipe systems hinges on a synergy between pipe strength and the surrounding soil support. Design procedures already integrate safety factors, emphasizing the vital role of proper installation in ensuring performance. Relying solely on increased pipe wall strength in design won't mitigate poor installation practices.
Learn MoreThe world of sanitary and storm sewers has seen a growing need for larger diameters to carry water. As pipe sizes increase, designing manway access becomes more challenging as larger pipes necessitate larger manholes or concrete boxes. It's not uncommon to resort to cast-in-place structures as the primary solution, which can be both time-consuming and expensive. However, with ongoing technological advancements and the increased use of thermoplastic pipe materials, alternative manhole solutions have been steadily gaining popularity. Many designers and regulators are recognizing the benefits of exploring alternatives to the traditional standard concrete manhole or box structures.
Learn MoreSUBSCRIBE
Get insights, news, tip & tricks delivered directly to your inbox